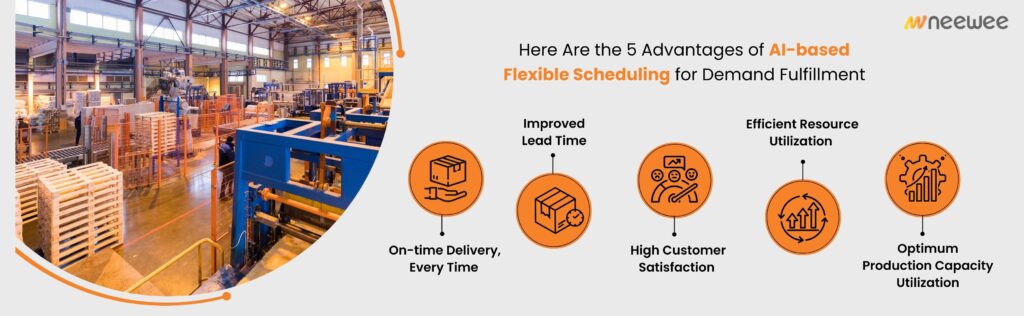
Predicting manufacturing defects and malfunctions in the process.
In quick succession to our story of how Neewee got listed as a Digital Twin Operator in an influential business and technology report, here is yet another. We are elated by the newest feather in our metaphorical hat!
The “Smart Factory Trend Report”, distributed by the Japanese TECHBLITZ, lists eight categories of digitalization services that will shape the future of manufacturing. We are proud to share that Neewee features as a representative in the ‘Design & Simulation’ category for our Digital Twin technology.
An article published online as a summary of the report points out that AI-powered design data visualization delivers accuracy in simulation. It also improves the iterative process efficiency. All crucial for product development.
Read the overview of the full report published here. 8 CATEGORIES OF SMART FACTORIES THAT ARE THE FUTURE OF MANUFACTURING – TECHBLITZ
Transformational Impact Through Connectivity
The industrial internet of things (IIoT) is the ecosystem of devices, people, and processes that are connected and interoperable. To briefly define the Digital Twin, it is a virtual representation of all those physical objects and processes in the entire manufacturing value chain. IIoT enables the data collection from various sensors, and Neewee’s AI app helps process it in real-time. The digital twin creates simulations of every step in the production process, unlocking valuable insights that help improve decision-making. The digital twin technology optimizes process efficiency in different manufacturing areas—product design and production to marketing— impacting business outcomes significantly. Thus, the potential for increased productivity using digital twins is immense as it transforms the entire industrial operations into intelligent manufacturing.
Neewee’s Digital Twin Technology for Predictive Analytics and Monitoring Production Performance.
Manufacturing is a cost-intensive and time-sensitive process. Predictive analytics in manufacturing can help companies forecast process variations, reduce waste, and control costs. Predictive analytics can also help manufacturers improve quality and provide more personalized customer service.
Dynamic, data-powered simulation of the physical world with the digital twin technology is a boon for predictive analytics. Getting an organization-wide view of shop-floor realities is key to effective decision-making. Statistical and analytical models help production managers predict and control future events in the process workflow. Predictive analytics uncovers patterns in production data to detect dysfunctional processes, which can cause anomalies in the output. Manufacturers can mitigate such risks if they receive timely actionable insights.
The digital twin also helps forecast deviations or disturbances in the manufacturing process before they occur. For example, if it predicts an issue with the equipment, an alert gets sent out to the production team. That helps them fix the equipment before the issue escalates and becomes an actual problem. The production team gets saved from unexpected downtime, which could have caused delays in batch-cycle time. Thus, a digital twin operator can help manufacturers save money by preventing any small or big interruption of the production line. Aside from monitoring production performance and catalyzing production flexibility, predictive analytics with the digital twin supports maintenance tasks too.
By aligning Neewee’s Digital Twin to the value you expect from your manufacturing processes, you can optimize production efficiency and enhance quality with a targeted approach.
Gartner’s survey revealed Digital Twins are entering mainstream use. Benoit Lheureux, research vice president at Gartner said, “Over two-thirds of companies that have implemented IoT will have deployed at least one digital twin in production.” This rapid growth in adoption is because digital twins are delivering business value and have become part of digitalization strategies. [1]
On the other hand, Thomas Kaiser, SAP Senior Vice President of IoT said, “Digital twins are becoming a business imperative, covering the entire lifecycle of an asset or process, and forming the foundation for connected products and services. Companies that fail to respond will be left behind.” [2]
You do not want to be left behind. Act now! Book a Demo.
For those who missed the detailed enumeration of “What Is a Digital Twin?” and the value it brings to manufacturing, read our previous post here Forrester Lists Neewee Amongst Digital Twin Service Providers in 2022 Report – Neewee
References:
[1] STAMFORD, Conn. (2019, February 9). Gartner Survey Reveals Digital Twins Are Entering Mainstream Use. Gartner. https://www.gartner.com/en/newsroom/press-releases/2019-02-20-gartner-survey-reveals-digital-twins-are-entering-mai
[2] Marr, B. (2017, March 6). What Is Digital Twin Technology – And Why Is It So Important? Forbes. https://www.forbes.com/sites/bernardmarr/2017/03/06/what-is-digital-twin-technology-and-why-is-it-so-important/?sh=1b2ef4c52e2a